Summary:Check valves serve to prevent backflow in systems by opening when pressure from upstream to downstream side builds up and closing when reverse pressure arises. There are various types of check valves, but swing and spring-type ones are the most popul......
Check valves serve to prevent backflow in systems by opening when pressure from upstream to downstream side builds up and closing when reverse pressure arises. There are various types of check valves, but swing and spring-type ones are the most popular because they're inexpensive yet effective at stopping reverse flow.
A swing check valve typically consists of three main components: valve body, disc, and hinge. The valve seat may be full-ported with an angle or straight-through configuration; linked to its hinge is a disc that moves when pressure from upstream forces it away from its valve seat for forward flow; when pressure from downstream drops off it moves back against its seat to stop reverse flow and close off the valve.
These types of check valves are typically preferred in water systems as they offer relatively low costs while providing sufficient backflow protection. Furthermore, they're an ideal choice in instances when space is at a premium or when vertical piping systems exist.
Installing swing check valves correctly requires several key considerations. First, ensure that the flange bolts are tightly fastened to avoid leakage. Second, place it where it can operate efficiently as a reverse flow could potentially strike and damage pipes or place additional loads on other components. Thirdly, ensure that the piping meets the appropriate size and pressure ratings to accommodate the check valve installation.
To maximize its potential, a swing check valve must be placed in a location free from obstructions such as other pipes, fittings, and pumping stations. This will prevent pressure buildup which could cause the valve to sag and close improperly; for optimal results, it should preferably be in a vertical orientation for optimal fluid dynamics in your system.
Pipe length ratios for swing check valves should include at least 10 pipe diameters of straight pipe upstream of the valve to ensure a laminar, smooth flow of liquid through it and prevent premature wear caused by spin and flow turbulence.
Swing check valves can be attached to pipelines in several ways, including flanging, threading, welding, or sweating. Each has its own set of advantages and disadvantages when selecting an appropriate method to attach it to the pipeline - choosing wisely will prevent leaks as well as facilitate removal for cleaning purposes when necessary.
K-value should also be taken into consideration when selecting a swing check valve, as this measurement enables engineers to calculate pressure loss through it. It is especially beneficial when conducting process flow calculations as this enables them to determine exactly how much loss of pressure will be necessary for any specific application.
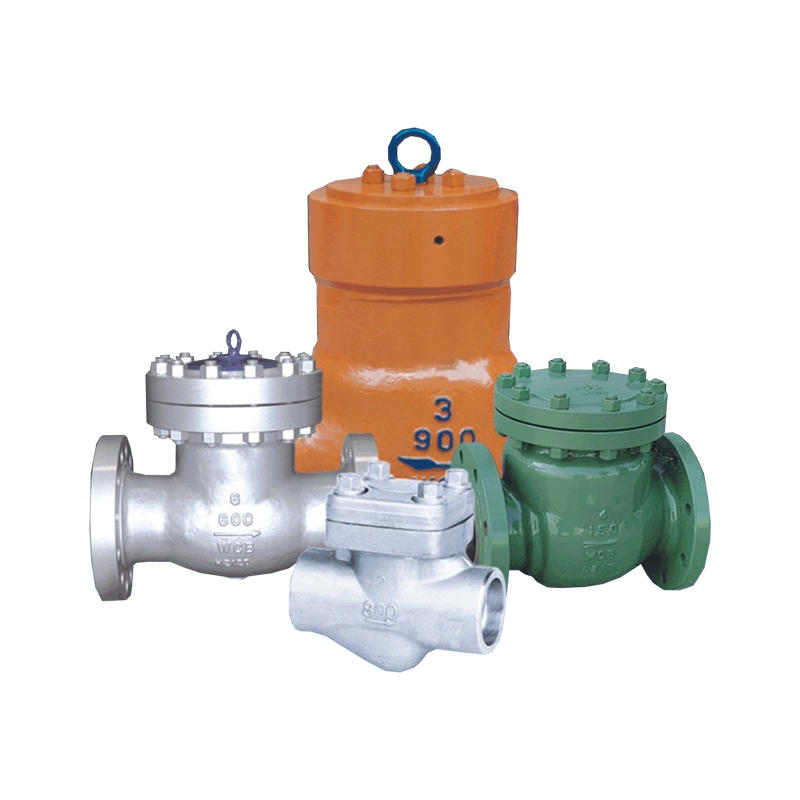