Summary:Ball Valves are a common type of valve used in a variety of applications. These valves use a hollow sphere to seal off passageways, controlling flow in industrial processes and other applications. They are also commonly used in plumbing, automotive a......
Ball Valves are a common type of valve used in a variety of applications. These valves use a hollow sphere to seal off passageways, controlling flow in industrial processes and other applications. They are also commonly used in plumbing, automotive and aerospace industries, among other sectors. Ball valves can be found in homes, offices, factories and other public spaces. Choosing the right one for your needs requires a thorough understanding of their construction, different types and key specifications.
In general, the main body of a ball valve is made of a material like steel, brass, bronze, cast iron or stainless steel. The body acts as the pressure vessel into which the other components of the valve are assembled. The body can be fabricated as a single piece or a multi-piece design. Multi-piece designs allow the body to be disassembled for repair and replacement when necessary.
The next component in a ball valve is the stem, which extends from inside the body and connects to the inner sphere. A packing system is usually placed around the stem and helps to ensure a tight seal, stopping media from leaking out of the valve externally. The stem is then connected to the valve’s actuator, which rotates it to open or close the valve. Actuation systems can be manual (handle or lever), electric, pneumatic or hydraulic.
There are two basic types of ball valves: float and trunnion. Floating designs feature the internal sphere “sandwich”ed between two seats that support it and keep it in place. When the valve is closed, the shaft connection to the inserted ball prevents it from moving laterally. Floating ball valves are generally the lowest-cost option and are well-suited to traditional on/off control applications in a variety of applications.
Trunnion valves, on the other hand, are typically more expensive than floating designs. They are designed for severe service applications where reliable, tight shut-off and fugitive emissions compliance are important considerations. They can withstand increased operating temperatures and pressures, which makes them an excellent choice for steam or high-purity chemical applications.
In addition to examining the specifics of each type of valve, users should consider the typical conditions they are expected to operate under. This will help them narrow down their choices to a valve that can provide the best performance in those conditions. ANSI ratings are commonly used to help customers compare ball valves in terms of the operating pressure they can safely handle. However, a PSI rating is not necessarily the same as an ANSI class rating.
While all valves are rated for their ability to hold up under certain conditions, it is important to understand how the ratings are calculated before making a purchase. This way, engineers can avoid selecting a valve that is overrated and will ultimately be costly to repair or replace. To learn more about selecting the right valve for your application, consult our article on Valve Selection. It includes a helpful table to illustrate the relationship between ANSI class, valve operating torque and other critical factors.
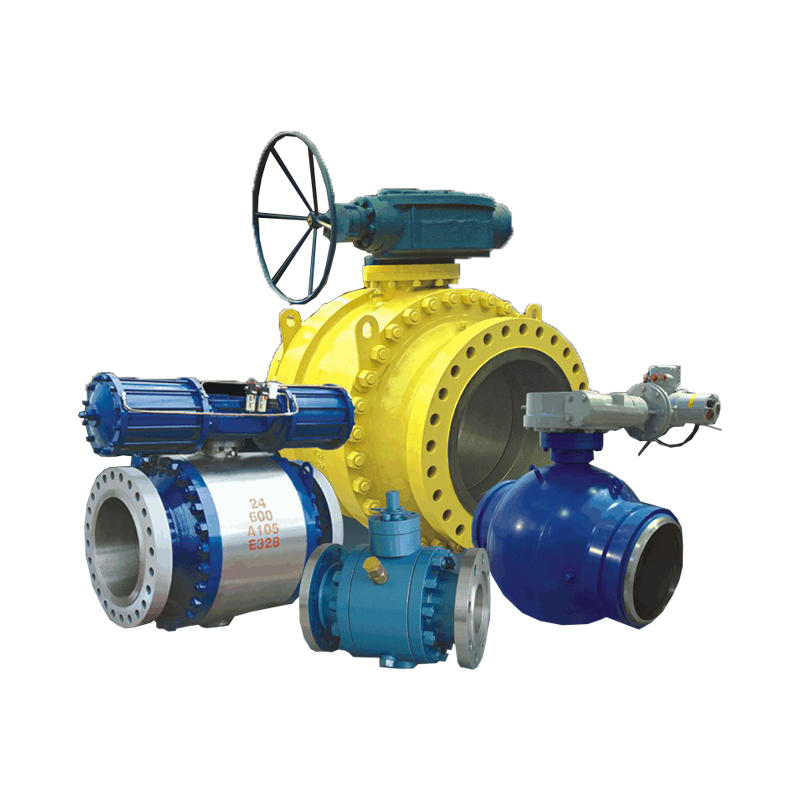